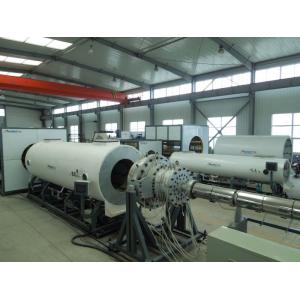
Add to Cart
gas/oil /water pipeline Puf Pre-Insulated Pipe PE shell casing plastic Machinery
Technical Prameters:
PE-365/760 | PE-420/960 | PE-850/1372 | PE-960/1680 | |
Main extruder | SJ-90/33 | SJ-90/33 | SJ-120/33 | SJ-150/33 |
Pipe diameter (mm) | Φ365-960 | Φ420-960 | Φ850-1372 | Φ960-1680 |
capacity (kg/h) | 550-700 | 550-700 | 700-900 | 800-1200 |
Installed power (kw) | 360 | 380 | 440 | 580 |
Length (m) | 35 | 36 | 40 | 48 |
HDPE Jacket pipe extrusion line for pre-insulated pipe is designed by Qingdao Huashida Machinery Co., LTD. It absorbs and improves developed HDPE pipe extruding technology.
The production line is an integration design composed by extrusion, vacuum calibrating, cooling, pulling, cutting, stacker. Great performance in automatic operation, extrusion capacity, steady and service life etc. Especially compared with the line use internal pressure method, vacuum calibrating method is much better than it for stiffness, pressure resistance and surface smooth.Vacuum calibrating method pre-insulation pipe outside casing extruded line is the advanced and popular machinery in the world.
Vacuum calibrating method pre-insulated pipe outside casing extrusion line is the most advanced and popular machinery in the world.In the practice of domestic construction becomes increasingly used energy-saving technology trenchless laying of pipelines, using pipes and fittings with industrial thermal insulation of rigid polyurethane foam (PUF insulation) in protective shell.
Pipelines PUF insulation intended for installation of heating networks with a working pressure of 1.6 MPa and a water temperature to 403 ° K (130 ° C) with a valid short-term increase in temperature to 423 ° K (150 ° C).
Piping PUF insulation and fittings is a rigid structure "pipe in pipe" consisting of steel or galvanized steel carrier pipe, a layer of polyurethane foam insulation and the outer jacket pipe protective of high-density polyethylene - for underground installation or sheet galvanized steel - for above-ground pad.
Rigidity due to the presence of strong ties between the steel pipe layer polyurethane insulation and jacket pipe and provides pre-shot blast or blast cleaning the surface of the steel pipe, optimum performance polyurethane insulation, corona surface of polyethylene pipe shell.
gas/oil /water pipeline Puf Pre-Insulated Pipe PE shell casing plastic Machinery Advantages:
Significantly increases the reliability of the pipeline in the PUF insulation system operational availability of remote condition monitoring PUF insulation, which allows to detect and repair leaking coolant, preventing accidents typical for thermal networks of other designs.
Highly cost-effective use of pipelines in the foam insulation define the following parameters:
Simplifying the construction, maintenance and repair;
Increased service life of 30-40 years (traditional types of pipelines - 5-10 years);
Reduction of heat losses to 8% (traditional types of pipelines - 30-40%);
Reducing capital costs by 15-20% (not required construction of concrete channels and chambers for valves);
Reduced operating costs by 9 times;
Reduction in repair costs 3 times.